Upfront simulation of the core pins’ deformation helps choose the mold materials
SIGMASOFT ® Virtual Molding provides a variety of methods to forecast the shrinkage and warpage of plastic parts. It is also possible to simulate the deformation of inserts or core pins during filling. SIGMASOFT® simulates and compares the deformation of core pins made of different materials under equal process conditions. The calculations are based on the imbalanced melt flow inside the cavity and the mechanical properties of the two materials.
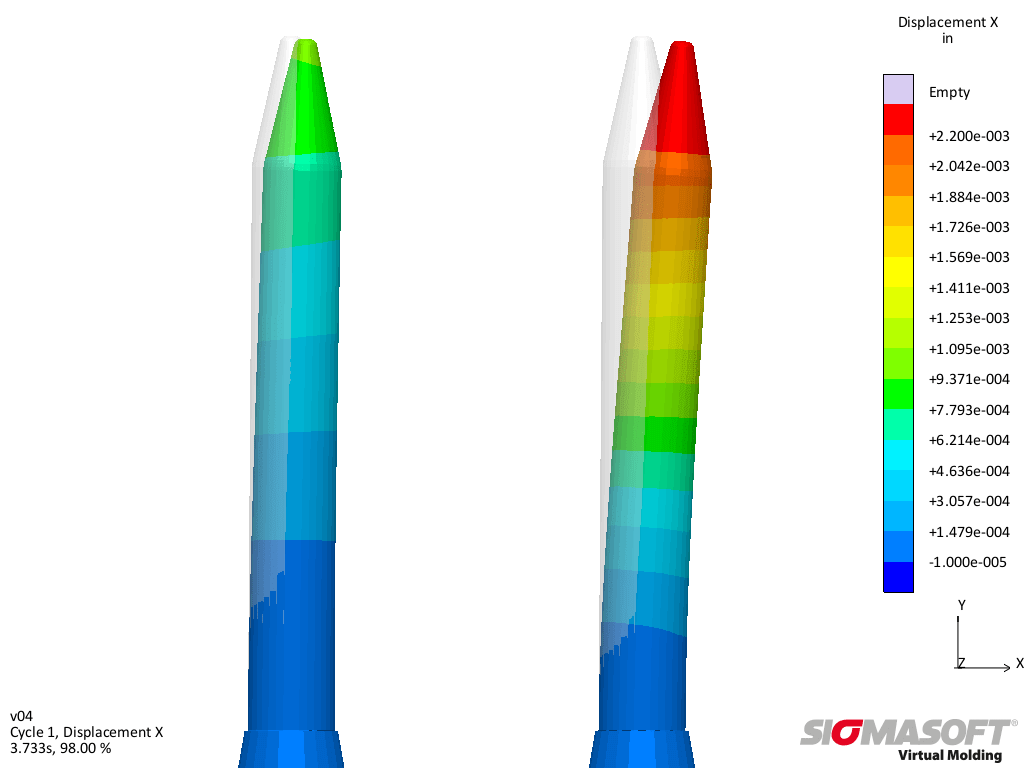
There are many questions injection molding manufacturers confront daily regarding the variety of materials available in the market. What type of steel should be used for which part of the mold? Whether it is the thermal conductivity of the steel used for the cavity insert, the diameter of a suitable ejector pin, or even the mechanical stability of the core pins, SIGMASOFT® Virtual Molding leads to the correct decision.
In SIGMASOFT® every mold material, e.g. steel, isolation, etc., is taken into account with its thermal and mechanical properties. As an example, it is possible to simulate the heating-up phase or the development of hotspots during several injection cycles having the thermal conductivity and specific heat capacity of all the mold materials. Besides the prediction of shrinkage and warpage of plastic parts, SIGMASOFT® also simulates the deformation of inserts and core pins during filling. These calculations are based on possible imbalances in the filling of the cavity and of course the mechanical properties of the steel.
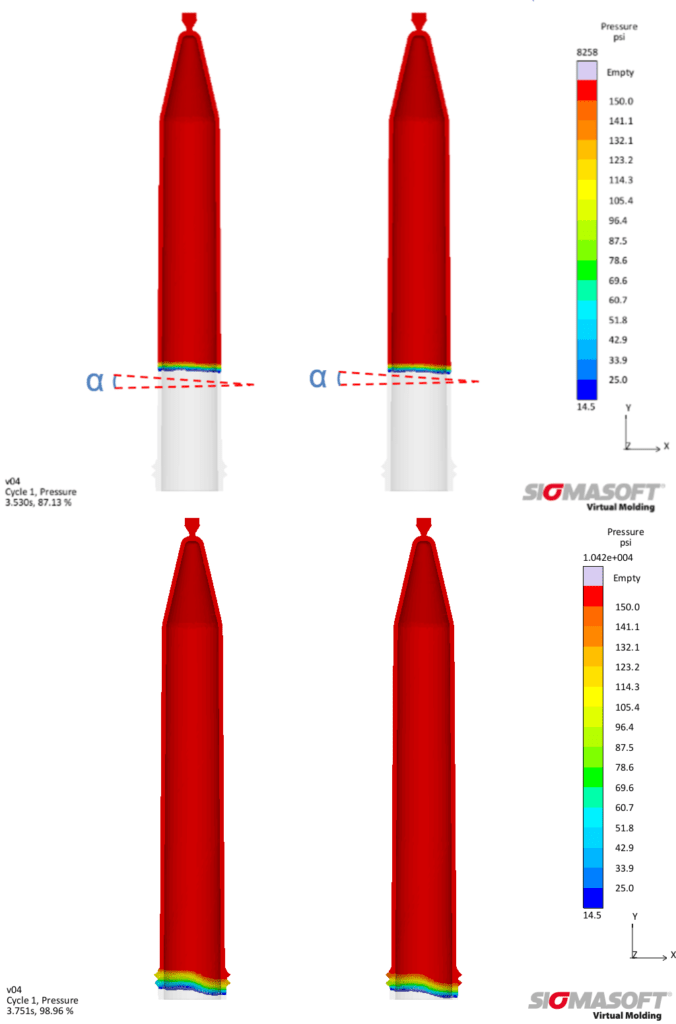
SIGMA Plastic Services, Inc. (IL), simulated an interesting project in cooperation with CAVAFORM (FL) and Crafts Technology (IL). In the project, the deformation of core pins, made of different materials, during filling of the cavity was evaluated. The investigation was done for an injection mold with 16 cavities, which is used to produce centrifuge tubes. In 8 of these cavities, core pins made of tungsten carbide are integrated to form the inside of the tubes. 420 stainless steel is used for the other 8 core pins. The analysis of the simulation results during the filling phase shows an imbalance, which existence after about 85% of filling has passed and becomes more obvious near the end of filling (Figure 2). This imbalance is caused by the asymmetrical geometry of the screw in the cap area of the tube and leads to a force, which tends to deform the core pins during the filling of the cavity. Due to the lower module of elasticity of 420 stainless steel, pins made of this steel are deformed about 3 times more compared to the pins made of tungsten carbide (Figure 1).
The described case is an example of the many details of injection molding, that can develop issues during the mold design phase. SIGMASOFT® Virtual Molding provides even the most experienced manufacturers with detailed insight into the injection molding process. With very low effort and based only on the thermophysical and mechanical phenomena, before ordering the mold, it is possible to examine and evaluate the effect of changes in the mold. Simulation provides a sound basis for decisions and supports the mold design from the beginning.